Experimental validation and calibration techniques
A numerical or analytical model of a physical process needs to be compared against experimental results, to validate that the model indeed describes the physical reality and to calibrate its parameters. To validate the models I develop, I have close collaborations to experimental facilities such as AFM, nanoindentation, μ-shear testing, computer tomography, selective laser sintering, and positron emission particle tracking.
In collaboration with the University of Siegen, frictional forces between small borosilicate particles were measured in a nanoindenter setup with very high accuracy, see figure; in particular a novel method was introduced to measure torsion friction, rolling a particle along an inclined rail cut into a surface by a Focussed Ion Beam. Several experimental techniques have been used in this process: Atomic force microscopy for measuring elastic and pull-off forces of particle-surface contact; a nanoindenter for measuring fores under simultaneous normal and tangential displacements; and etching to modify the surface roughness [J13,C3].
(Left) Atomic force microscope and (Right) Nanoindenter at the University of Siegen.
(Left) Rail cut into a surface by a Focussed Ion Beam.
(Right) Surfaces are edged to produce different roughnesses.
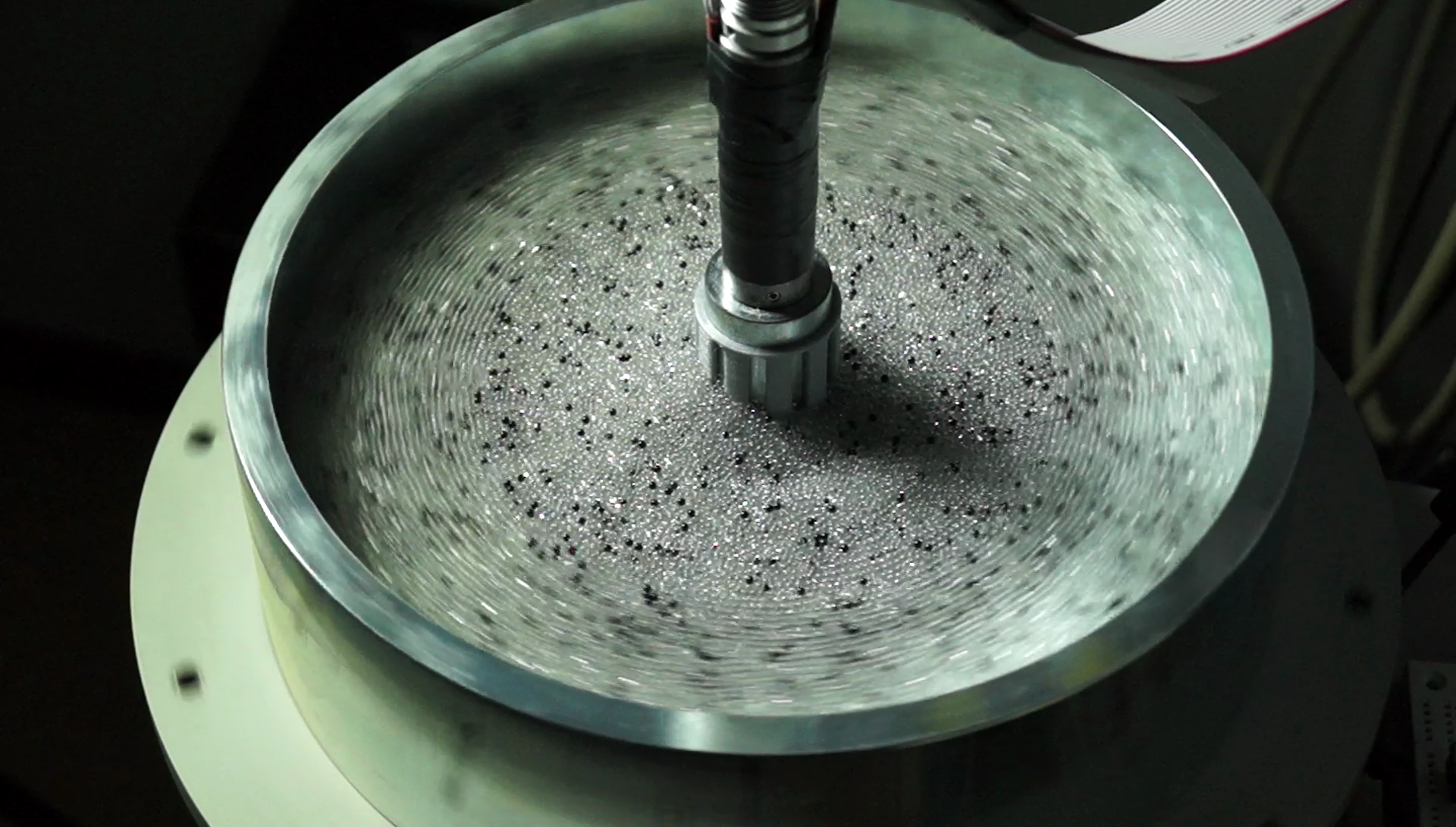
The rheology of particles under quasistatic shear is strongly dependent on the amount of cohesion. This has been tested in a split-bottom shear cell by my PhD student S Roy, see figure, and compared to the rheological model [J14,C5,C4]; a publication of the results will be available soon.
To study the effects of sintering of soft, plastic materials, a polystyrene particle bed is sintered and its elastic properties are measured [C9,S5].
(Left) SEM image of sintered particle-surface contact (polystyrene-Si(100)).
(Centre) In-situ nanoindentation and confocal microscopy setup;
(Right) Real-time confocal microscopy image series during nanoindentation.
Designing new experiments is a difficult, time-consuming and expensive process. The construction of a new apparatus typically takes several months from inception to the final product, with no guarantee of success. In our fast-evolving research fields, such delays are clearly undesirable, and can severely hinder research efforts. This process can be advanced using Rapid Prototyping to build experimental setups, or to print particles of a desired shape. In collaboration with L Orfice from the Research Center Pharmaceutical Engineering (RCPE) Graz, we use Rapid Prototyping to study the behaviour of a screw feeder.
A) 3D-printed scale model of screw feeder, B) Particle flow simulation using MercuryDPM
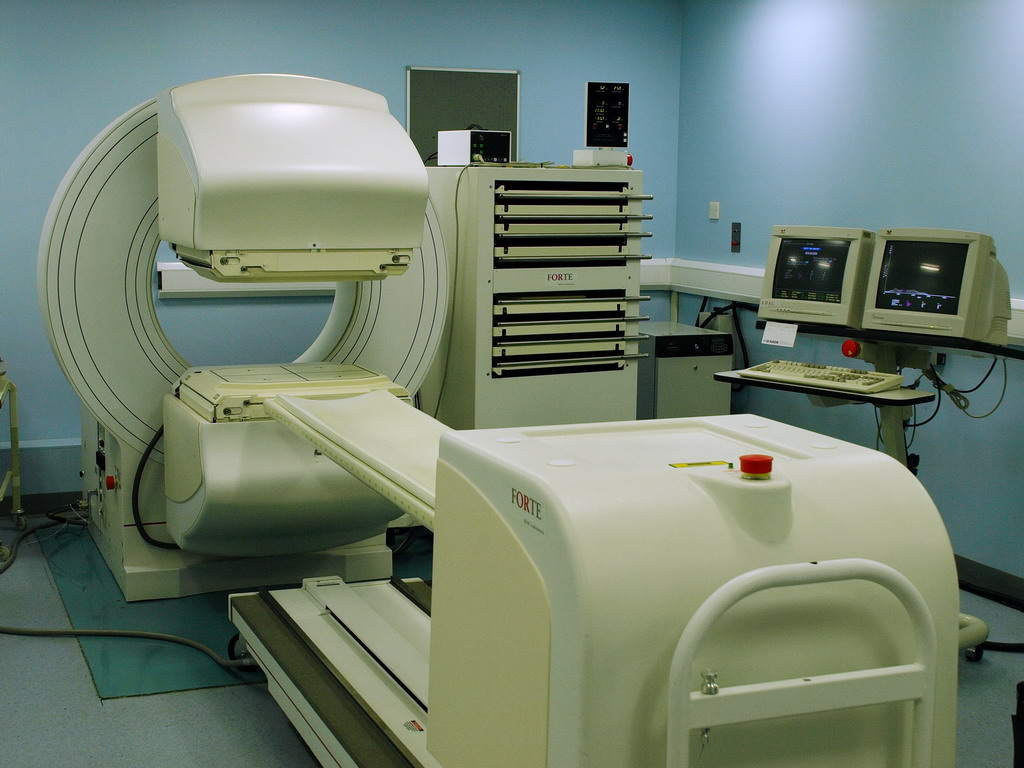
Real industrial systems are often difficult to observe: Visual observation is often not possible, due to the obstruction by the opaque boundaries of the apparatus, or the equipment-unfriendly conditions (heat, pressure) inside. Positron Emission Particle Tracking (PEPT) scanning is a technique that allows an unintrusive look inside real equipment, by tracking individual particles that have been modified to emit gamma rays. In a collaboration with K Windows-Yule and D Parker, segregation behaviour has been studied using the PEPT scanners and synchrotron facilities at the University of Birmingham [J12,J10].